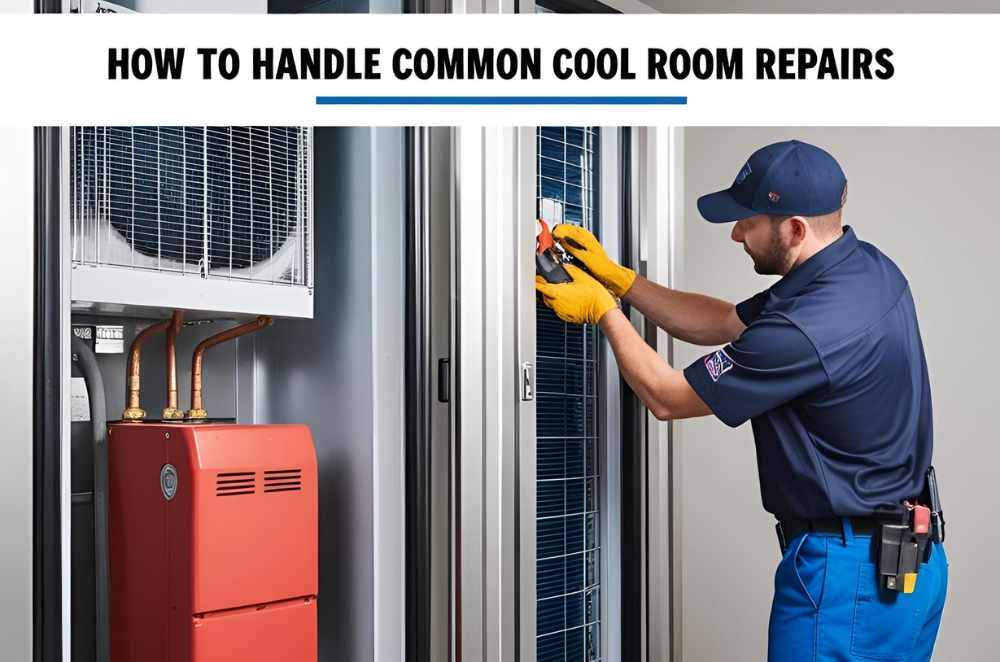
Cool rooms are the silent backbone of countless Aussie businesses, from busy cafés to industrial food suppliers. But they tend to do so without much warning when things go wrong. A sudden temperature spike or strange noise can quickly become thousands of dollars in lost stock or health compliance breaches.
That’s why it's essential to stay on top of maintenance and understand the most common repair issues. Whether you're managing a warehouse or a small bar, the principles are the same: early detection and timely intervention.
Take, for example, a client I worked with recently who ran a high-volume restaurant in the Inner West. They didn’t realise their cool room compressor was failing until it finally gave out during the weekend rush. The fallout? Lost produce, frustrated staff, and a hefty emergency callout. Since then, they've partnered with a local technician who handles cool room repair with fast turnaround and specialist expertise.
Recognising the signs of cool room trouble early
Spotting problems before they escalate is half the battle. And trust me—I've seen firsthand how often early signs are ignored. A bakery I consulted for kept dismissing small puddles forming near the door as "just condensation." Turns out, the door seal had warped from repeated slamming. Their energy bills had jumped 30% by the time they addressed it.
Common warning signs include:
Uneven cooling or frost on the back walls.
Water is pooling on the floor.
Door hinges are not aligning or closing fully.
Loud humming, rattling, or clicking noises.
Even subtle changes, like products not feeling as cold or the fan running nonstop, should raise a red flag.
Tips for staying ahead of issues:
Train staff to spot and report minor irregularities.
Check the seal and hinges weekly.
Monitor digital thermometers or consider smart sensors.
Don’t ignore minor puddles or strange smells; they often indicate a deeper issue.s
Top repair problems and what causes them
Over the years, I've noticed that most service calls involve the same core issues. While the equipment might vary slightly across industries, the repair patterns remain surprisingly consistent.
Door seal failures – The number one offender. A worn-out seal lets warm air in, triggering frost build-up and system strain.
Fan motor burnout – Usually due to dust build-up or age, this affects airflow and leads to inefficient cooling.
Blocked drainage or evaporator coils – Often caused by a lack of cleaning or overly humid environments.
Thermostat misreads – These can cause false readings and overcooling or undercooling issues.
Refrigerant leaks – A more serious issue, usually involving noticeable performance drops and icing.
In many cases, basic upkeep can avoid these. But when ignored, they often lead to larger system failures and expensive part replacements.
Quick wins to avoid repairs:
Keep coils clean and dust-free.
Don’t overload the space—air needs room to circulate.
Clean evaporators monthly.
Book biannual check-ups with a qualified tech.
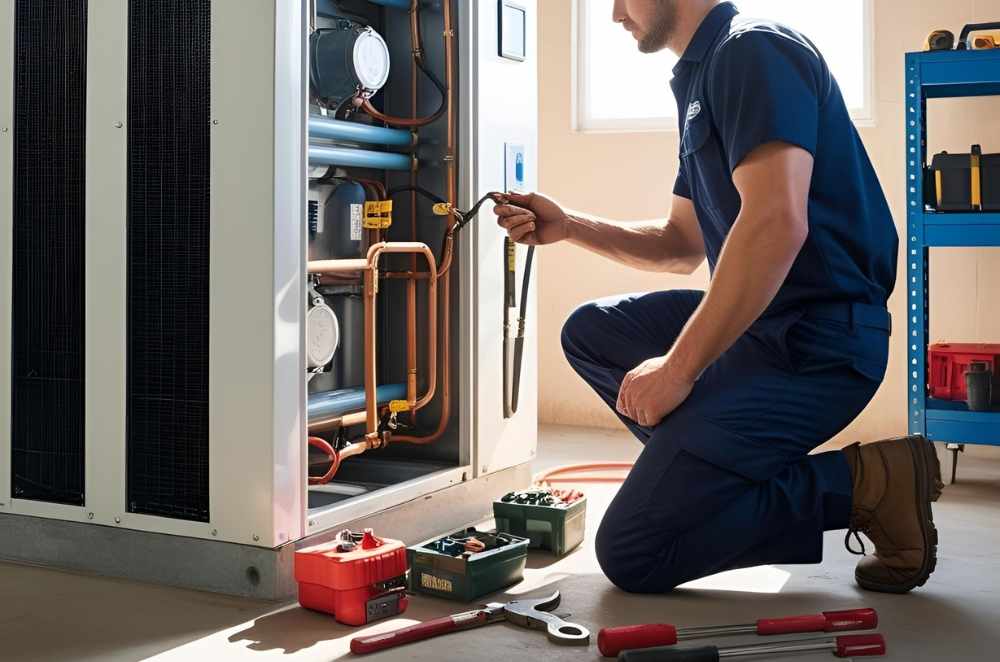
Understanding the repair process
Cool room repairs can range from quick fixes to full-scale component replacements. Understanding what to expect helps demystify the process.
Inspection & Diagnosis: The technician assesses the room's performance, looking at temperatures, seal conditions, electrical components, and refrigerant levels.
Quotation & Approval: You’ll get a quote for parts and labour once diagnosed.
Repair or Replacement: This could range from resealing a door to installing a new thermostat or fan motor.
Testing & Sign-Off: After repairs, the system runs at its own pace to ensure full functionality.
Depending on part availability, most issues can be resolved within a few hours or a day. For larger commercial setups, repairs might be staggered or involve temporary cooling solutions.
Proper record-keeping during this process is also vital, especially for businesses in the food and beverage industries. Safety standards are no joke, and refrigeration systems are considered plant equipment under national guidelines.
In fact, refrigeration safety standards from Safe Work Australia specify requirements around electrical safety, accessibility, signage, and regular maintenance schedules.
The role of preventative habits in long-term savings
You’ve heard it before: prevention is better than a cure. But in refrigeration, it’s also cheaper.
One logistics warehouse I advised switched from reactive to preventative maintenance, with just quarterly check-ups and weekly in-house inspections. Within six months, their repair frequency dropped by 80%, resulting in less downtime, fewer emergency costs, and better energy efficiency.
Here's what you can start doing:
Schedule monthly cleaning of all accessible parts.
Use plastic strip curtains to limit air exchange.
Keep inventory away from fans and walls.
Create a simple logbook or checklist for staff.
Energy efficiency is another bonus of staying on top of your maintenance. Even minor tweaks like adjusting shelf layout or limiting door openings can make a noticeable difference in your electricity bills.
External insights worth exploring
Gaining an outside perspective can enhance your strategy, no matter how effectively you manage things. Maintenance isn’t just about reacting to issues—it’s about creating a system that runs smoothly and seldom breaks down in the first place. There’s always room for optimisation, whether through scheduling reminders, implementing cloud-based logging systems, or providing comprehensive staff training. We highly recommend exploring preventative maintenance best practices for valuable insights. This resource offers practical strategies for maintaining cool rooms and HVAC, electrical, and food-handling systems.
In summary, Cool room issues are avoidable
If there’s one takeaway, it’s this: most cool room disasters start as tiny, fixable problems. A cracked seal, a dusty fan, and a laggy thermostat are all manageable if caught early.
What matters is acting before those problems snowball.
Having a regular maintenance plan, training staff to spot warning signs, and working with experienced pros, especially those familiar with marvellous room repair, gives your business the edge it needs to avoid significant disruptions.
Stay ahead, stay cold, and keep those fridges humming.
Write a comment ...